Expert Guidance on What is Porosity in Welding and Just How to Address It
Expert Guidance on What is Porosity in Welding and Just How to Address It
Blog Article
Porosity in Welding: Identifying Common Issues and Implementing Ideal Practices for Avoidance
Porosity in welding is a prevalent issue that typically goes undetected up until it creates substantial troubles with the integrity of welds. This usual issue can endanger the strength and durability of bonded structures, positioning security risks and causing pricey rework. By comprehending the origin of porosity and carrying out reliable prevention methods, welders can dramatically improve the high quality and integrity of their welds. In this discussion, we will certainly check out the essential factors adding to porosity development, analyze its harmful effects on weld performance, and discuss the very best methods that can be embraced to lessen porosity occurrence in welding processes.
Usual Causes of Porosity

Utilizing filthy or wet filler materials can introduce impurities into the weld, adding to porosity concerns. To mitigate these typical causes of porosity, complete cleaning of base steels, appropriate shielding gas selection, and adherence to ideal welding parameters are essential methods in achieving top quality, porosity-free welds.
Effect of Porosity on Weld High Quality

The presence of porosity in welding can substantially jeopardize the architectural integrity and mechanical residential or commercial properties of welded joints. Porosity develops gaps within the weld metal, damaging its overall stamina and load-bearing ability. These gaps serve as stress concentration factors, making the weld much more susceptible to splitting and failing under used tons. Additionally, porosity can minimize the weld's resistance to deterioration and various other environmental elements, further decreasing its long life and performance.
One of the main consequences of porosity is a reduction in the weld's ductility and sturdiness. Welds with high porosity levels have a tendency to exhibit reduced effect toughness and lowered ability to flaw plastically prior to fracturing. This can be especially worrying in applications where the bonded parts are subjected to dynamic or cyclic loading conditions. Porosity can restrain the weld's ability to successfully send forces, leading to premature weld failing and prospective safety and security hazards in important frameworks. What is Porosity.
Ideal Practices for Porosity Prevention
To boost the architectural integrity index and quality of bonded joints, what specific actions can be applied to lessen the event of porosity during the welding process? Utilizing the proper welding strategy for the certain product being welded, such as adjusting the welding angle and weapon position, can further avoid porosity. Routine examination of welds and immediate remediation of any kind of concerns determined throughout the welding procedure are vital practices to avoid porosity and generate high-grade welds.
Relevance of Proper Welding Techniques
Executing correct welding strategies is paramount in making certain the architectural integrity and high quality of bonded joints, building on the foundation of effective porosity prevention actions. Welding strategies directly affect the general strength and sturdiness of the welded structure. One crucial element of correct welding strategies is maintaining the proper warmth input. Extreme warmth can cause boosted porosity as a result of the entrapment of gases in the weld pool. Conversely, insufficient warm might cause incomplete combination, creating prospective powerlessness in the joint. Additionally, using the ideal welding criteria, such as voltage, existing, and travel rate, is important for accomplishing sound welds with minimal porosity.
Additionally, the option of welding procedure, whether it be MIG, TIG, or stick welding, must straighten with the details demands of the job to guarantee optimum results. Proper cleaning and preparation of the base steel, along with selecting the appropriate filler material, are additionally necessary elements of competent welding useful content techniques. By sticking to these ideal practices, welders can lessen the threat of porosity formation and produce top notch, structurally sound welds.
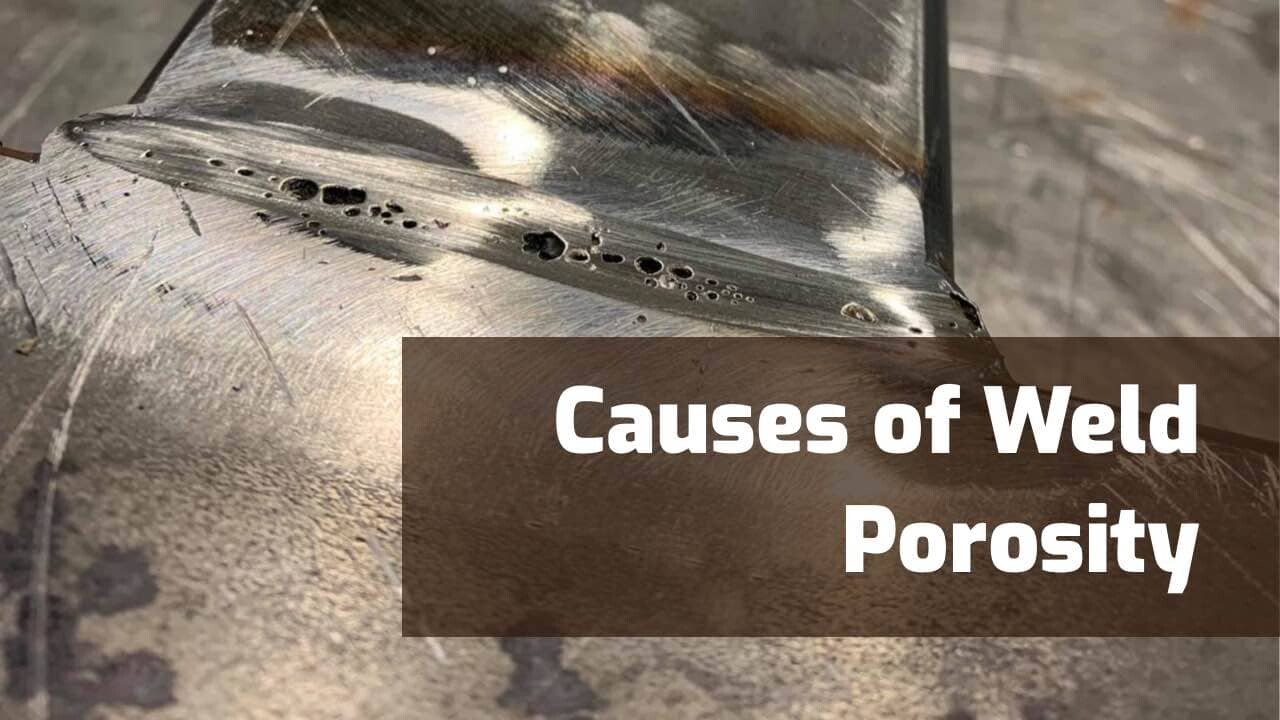
Testing and Quality Assurance Actions
Quality control procedures play a crucial function in confirming the honesty and reliability of More Info welded joints. Checking treatments are necessary to spot and stop porosity in welding, ensuring the strength and sturdiness of the last item. Non-destructive screening approaches such as ultrasonic screening, radiographic testing, and visual inspection are typically utilized to determine prospective flaws like porosity. These strategies permit the assessment of weld top quality without jeopardizing the stability of the joint. What is Porosity.
Post-weld examinations, on the other hand, analyze the final weld for any issues, including porosity, and validate that it meets specified requirements. Applying a comprehensive top quality control plan that consists of thorough screening treatments and evaluations is critical to lowering porosity problems and making certain the total quality of welded joints.
Final Thought
In verdict, porosity in welding can be a common issue that affects the top quality of welds. By recognizing the usual causes of porosity and executing finest techniques for avoidance, such as correct welding techniques and testing steps, welders can guarantee high top quality and trusted welds. It is vital to prioritize prevention methods to reduce the incident of porosity and preserve the honesty of bonded frameworks.
Report this page